Introduction
In the agro-food manufacturing world, equipment reliability is as critical as food safety. A well-maintained pulses processing line can run continuously, deliver consistent output, and extend machinery life by several years. Whether you process lentils, chickpeas, peas, or beans, adopting a proactive maintenance strategy protects your investment and ensures you meet production goals.
At Alloy Industrial Sourcing, we support clients with robust machinery and the operational strategies to keep them running at peak efficiency. This guide explores the best practices, schedules, and technologies to maximize uptime and minimize mechanical wear.
Why Maintenance Is Crucial in Pulses Processing
1. Avoiding Costly Downtime
Unexpected machine failures can halt production, delay deliveries, and impact contractual obligations. Unplanned downtime is not just an inconvenience—it’s expensive.
2. Ensuring Consistent Quality
Loose bolts, clogged airflows, or uncalibrated sorters can lead to:
•Inconsistent cleaning or grading
•Over-rejection of usable product
•Contamination risks
3. Extending Equipment Life
Routine servicing ensures longer lifespans for critical machinery like:
•Optical sorters
•Gravity tables
•Aspirators and polishers
•Magnetic and destoning systems
Core Maintenance Principles for Pulses Lines
A. Preventive Maintenance
Scheduled servicing regardless of performance symptoms. It includes:
•Lubrication
•Filter cleaning/replacement
•Belt alignment
•Sensor calibration
B. Predictive Maintenance
Using data from sensors and software to anticipate issues before they cause failure. Examples:
•Vibration monitoring on motors
•Heat sensors on bearings
•Airflow pressure drops in aspirators
C. Corrective Maintenance
Repairs and replacements triggered by unexpected faults. While sometimes unavoidable, the goal is to minimize frequency through the above methods.
Recommended Maintenance Schedule (Sample for 1 Shift/Day Operation)
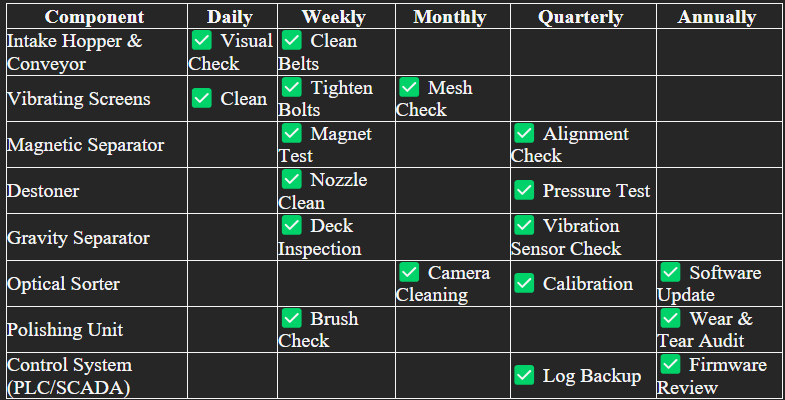
Note: This schedule should be adjusted for multi-shift operations or harsh environments.
Tools & Technology to Support Maintenance
1. Digital Maintenance Logs
Record completed tasks, technician notes, and upcoming schedules. Can be paper-based or cloud-integrated with the control panel.
2. IoT-Based Monitoring
Smart sensors can detect anomalies in real time, reducing reliance on visual checks.
3. Remote Diagnostics
With Alloy’s SCADA-connected systems, engineers can troubleshoot or even initiate calibrations remotely.
Spare Parts Management
A. Critical Components to Stock On-Site:
•Optical sorter ejectors
•Motor belts and bearings
•Screen meshes
•Air filters
B. Suggested Spare Parts Policy:
•Maintain minimum 2-week buffer stock
•Implement First-In-First-Out (FIFO) rotation
•Conduct biannual inventory audits
Alloy Industrial offers fast-shipping spare parts and inventory planning support.
Staff Training & Maintenance Culture
Your line is only as reliable as the people maintaining it. Training operators and technicians to recognize early signs of wear or misalignment can:
•Prevent larger failures
•Improve inspection speed
•Create ownership culture across shifts
Alloy provides hands-on training during installation and refresher programs on request.
When to Upgrade Instead of Repair
Even with good maintenance, machinery eventually becomes obsolete. Consider upgrades when:
•Spare parts are discontinued
•Energy consumption is too high
•Product specs change and new features are needed
•Quality rejection rates increase despite tuning
Alloy offers upgrade assessments and phased modernization strategies.
Efficient pulses processing doesn’t stop at installation. A disciplined maintenance program is essential for protecting your investment, ensuring food safety, and maximizing profitability.
Whether you operate a 2TPH line or a 10TPH facility, Alloy Industrial Sourcing provides both the technology and guidance to keep your operations running smoothly.
Contact us today to request a maintenance consultation or spare parts checklist tailored to your plant.